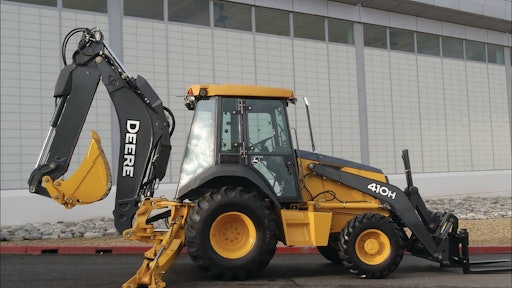
Husco Intl.'s INCOVA technology represents a radical departure in the way hydraulic systems operate, offering OEMs and their customers improvements in six critical areas -- productivity, efficiency, controllability, reliability, safety and flexibility -- without adding to the total cost of the vehicle.
Husco began working toward what would become INCOVA (Intelligent Control Valve) seven years ago, when the R&D department brainstormed what it would take to create a hydraulic system that would be completely different. In the past, improving one aspect of the hydraulic system meant sacrificing another.
"By first starting with a clean sheet of paper and focusing on how to increase the six critical customer areas," says Chris Kolbe, vice president of sales and marketing, Husco Intl., Waukesha, WI, "we were able to identify the spool as a main limitation in preventing any significant change."
Because the orifices in a spool valve are tied to each other, there are no degrees of freedom as they cannot operate independently. The old spool valve was tossed onto the scrap pile.
After further development, in its place went an intelligent valve comprised of four independently controlled Electrohydraulic Poppet Valves (EHPV), in a layout similar to a Wheatstone bridge electronic circuit. The zero-leakage EHPVs provide bi-directional metering and metering modes.
"The real breakthrough was the zero-leak proportional control poppet valve which provides for independent meter-in meter-out operation," says Kolbe. "We worked on its development for a long time." The EHPV was completed and patented about three years ago. It's the hardware-enabling piece in the system, but the software is really the heart of the system.
"Once you go to electronics in a hydraulic system all of your customized controllability is in the software. This trend is changing the industry in the same manner INCOVA is altering the way Husco operates. "Now we have more patents on software than we do on our hardware," says Kolbe. "We have grown our staff of engineers who are focused on electronics and controls design significantly, where previously the great majority of our staff was mechanical engineers."
INCOVA's distributed electrohydraulic configuration is enabled by an integrated controller containing transducers which measure the pressures at the cylinder. This measurement allows the system to tell the pump what the pressure should be, enabling the system to provide electronic load-sensing and pressure compensation.
The distributed INCOVA valves are mounted out on the cylinders, eliminating more than 50% of the fittings and hoses that are required on a traditional hydraulic system. One of the benefits to this is the reduction of pressure loss in the hoses.
"At the end of a telehandler boom you'll have a cylinder for the fork," says Kolbe. "The flow has to travel from the pump through all that hose to get to the control valve." With the INCOVA system hydraulic fluid can be routed from one side of the cylinder directly to the other, travelling less than a foot. "It's the same idea as if you plug in about 200 ft. of cord to run a weed whip, it won't get enough power to operate. You can lose a lot of efficiency throughout the length of the hose."
Because hydraulic oil is going from one side of the cylinder to the other, the pump is not required to supply as much oil. The pump doesn't need to be as big, less heat is generated, and the entire system can require less oil.
Distinct advantages
With a changing workforce and the reduction of expert vehicle operators, electrohydraulics are increasingly being used to automate functions that could only be achieved by an expert operator in the past. "Manufacturers have been trying to utilize electronic-controlled hydraulics for a long time," says Kolbe, "but the problem is it has been very expensive. The INCOVA system reduces the system complexitity and cost by reducing the number of components, fittings, hosing, vehicle structure and horsepower requirements. The cost impact of adding electronic controls is nominally equivalent to pilot controls." Plus, INCOVA can increase customer value in six critical areas:
Productivity: The system can help reduce vehicle cycle times by up to 50%. The design allows for multiple metering configurations, including gravity lower regeneration. In this, oil on the piston side of the cylinder is routed to the rod side of the cylinder, and no pump flow is consumed. The lowering speed is not limited by hydraulic pump size.
Efficiency: INCOVA's special metering mode allows hydraulic functions to operate without pump flow, when gravity can supply the energy. Since INCOVA eliminates load-holding valves, their attendant power losses are prevented. The distributed system also allows flow regeneration at the cylinder, reducing line losses.
Safety: Integrated pressure transducers allow the system to control the acceleration and deceleration of loads. On a telehandler, the most common accident occurs when a full load is quickly raised and suddenly hits the end of the stroke. The resulting jolt can tip the machine backward. "Because INCOVA is measuring the position of the cylinder, we can tell when the cylinder is at full stroke and slow it down." If the machine loses electrical power, the fail safe condition is to shut off, locking the machine in position.
Controllability: On a telehandler, for example, the operator often moves more than one actuator at a time. Hydraulic systems can encounter cross-talk between the control and load-holding valves that result in a chattering in the cylinder. INCOVA's distributed valve acts as the control valve and load-holding valve, eliminating cross-talk. Coordinated X-Y motion is achievable, as well.
Reliability: By reducing the number of fittings and the length of plumbing required, INCOVA helps reduce the main warranty issue for most OEMs. On a telehandler, the length of plumbing can be reduced by 50% and the number of fittings by 30%. The system's individual components are built to Husco's strict design practices to ensure reliable products.
Flexibility: With the distributed topology, there are only two hoses in a telehandler boom, the pressure and tank lines. Valves and features can be added with ease. The system utilizes a J1939 CAN bus system. Four small wires go up the boom, which allows the customer to put electronics out on the end of the boom, such as a joystick.
Cost: The INCOVA system is less than or equal to a traditional pilot-operated hydraulic system, while providing features that would not otherwise be possible. This is accomplished by eliminating many of the components found in a traditional system.
Total machine control
Understanding INCOVA requires the customer to think about hydraulic systems in a new way. Husco began the educational process at two separate booths at ConExpo in Las Vegas earlier this year. "One of the best things about ConExpo is that you get OEMs and end-users in the display areas, where they could operate the INCOVA-equipped telehandler we had on display," says Kolbe. "While the end-users might not know the ins and outs of hydraulics, they immediately notice that the system is smoother, easier to use, and more controllable.
"When you're developing new technology it is good to have the confirmation that it provides a value to the end customers of the machines."
The construction and material handling industries are major targets for INCOVA. John Deere will be the first OEM to offer the system on its 410H loader-backhoe this fall. INCOVA will be part of Deere's Total Machine Control system.